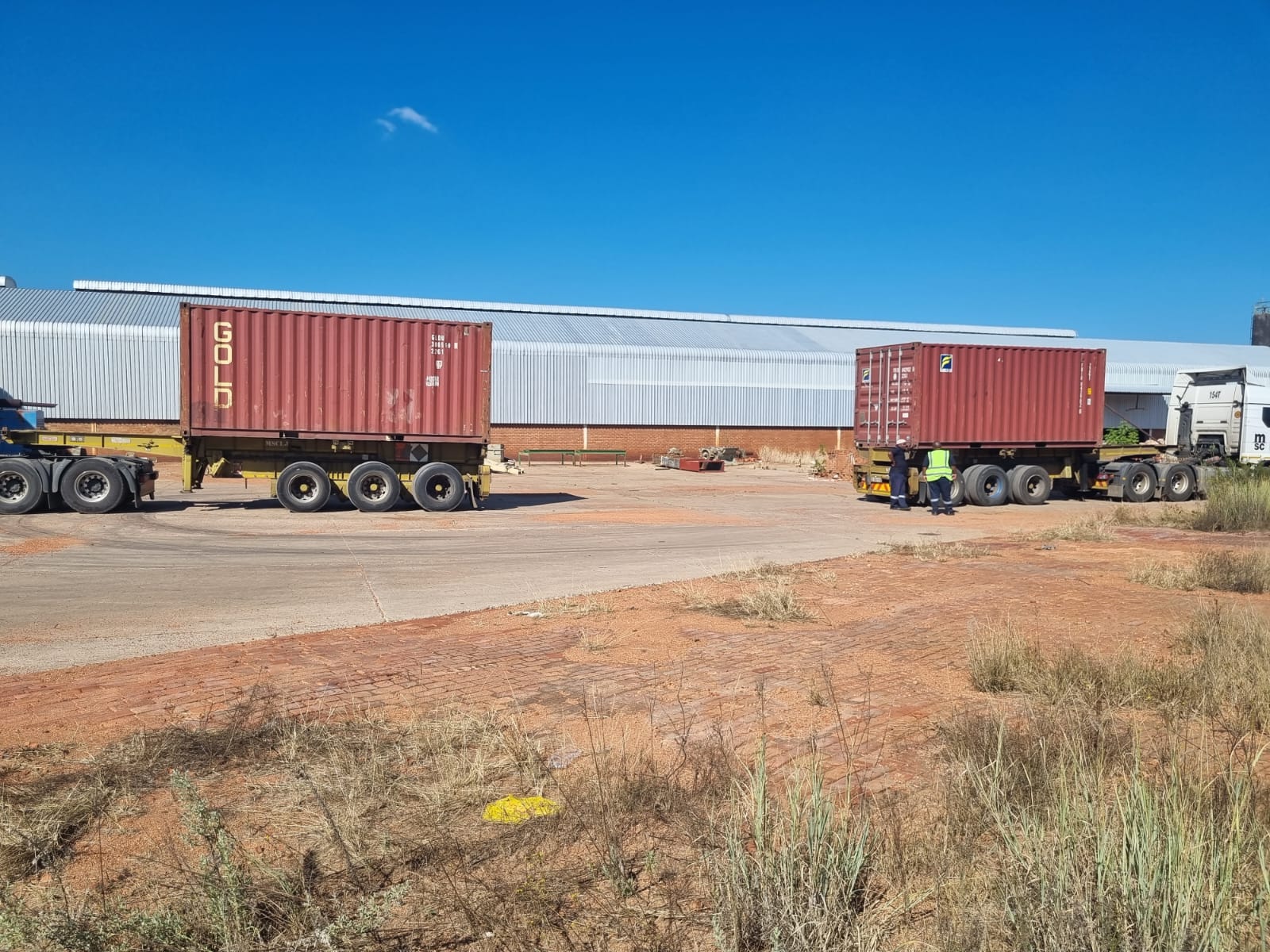
Refractory industry in recent years has witnessed a dramatic increase in the cost of virgin raw materials. This has been largely due to increasing development in the Asian market, particularly India and China, where owing to domestic demand materials such as bauxite and magnesia are no longer readily available for export (Buhr and Spreij, 2009; Industrial Minerals; Hutton, Yates, and Green, 2009; Buhr et al., 2006; Schmidt-Whitely, 2008; Feytis, 2010; Tran, 2007; Wanecq, 2010; O’Driscoll, 2003; Saxby, 2012). In the 1990s low-priced Chinese bauxite replaced other alumina-bearing materials such as andalusite, mullite, and in some instances even chamotte. At that time it was easy for refractory suppliers to provide their customers with new refractories having higher alumina contents (Buhr and Spreij, 2009). The general perception was that a higher alumina content meant superior performance. For this reason, bauxite-based refractories became a preferred option where a higher alumina content was required. With raw materials being the major cost driver in the refractories business, many refractory producers outside China are facing an uncertain future. Escalating costs and falling quality of imported Chinese raw materials put local manufacturers at significant disadvantage compared to Chinese refractory producers, who can export to South Africa at zero rate import duties.
Source: www.scielo.org.za